Comparative instruments, such as an adjustable bore gage, can feature an electronic readout or dial that displays the direction and amount of variation in the test bore, from the nominal size. If you are using adjustable bore gages this way, you need to set the gage to the required nominal size, to which the bore is to be compared. There are various ways to set the bore gage to the nominal size. The methods explained below can provide a balance of versatility and reliability, precision, and speed. Read on to find out which setup method will work best for you:
Getting Your Adjustable Bore Gage Settings Right From The Get-Go
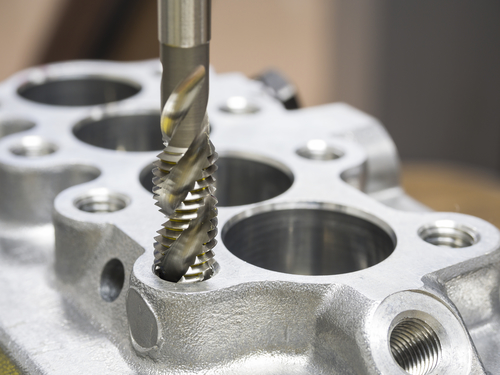
20
Nov