Strain measurement is capable of resolving one PPM (one part in a million) or more. This is because of the exacting controls and standards under which each strain gage is manufactured. Some of the principal measurement errors arise from the manner in which the strain gage sensor is installed and measurement is taken. Let us take a look at some of these.
What You Need To Know About Strain Measurement Errors
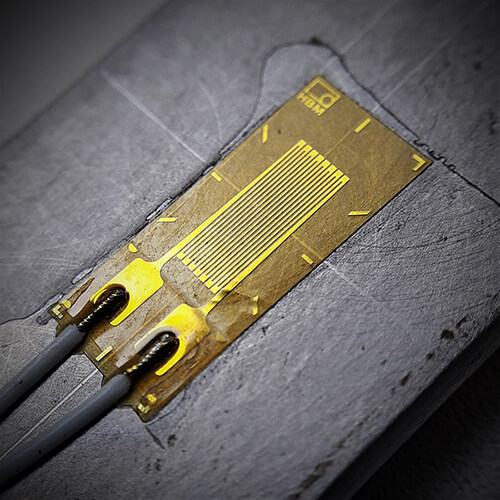
12
Apr