Parts manufactured by the aerospace and automotive industries are becoming more complex due to technology advancement. Tolerances that should keep up with metrology standards and quality control are now increasingly optimized and sophisticated. Moreover, customers need their dealers to ensure their own control in compliance. All these requirements put a lot of pressure on quality control teams and metrology. This post will explore how we can deal with constantly increasing pressure on tolerances. First of all, let’s take a look at the major reasons for evolution in quality control requirements in the aerospace and automotive industries.
Tackling The Issue Of Increasing Pressure On Tolerances
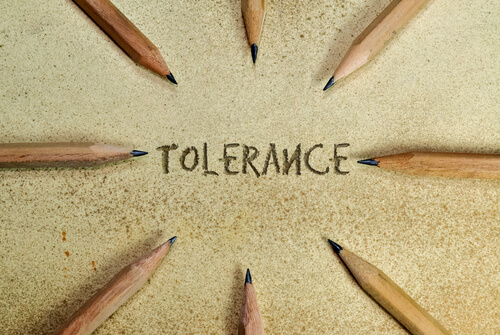
06
Dec