Today there is a growing trend towards miniaturization especially in the electronics, medical device and computer industries. If you are involved in one of these industries, you need to ask yourself which inspection system best meets your requirements. Between the contact and noncontact inspection systems, which type should you choose? The resurgence of match-fitting and selective assembly practices which depend on more precise measurement data, makes the question as timely as ever.
Understanding The Different Types Of Contact And Non-Contact Inspection Systems
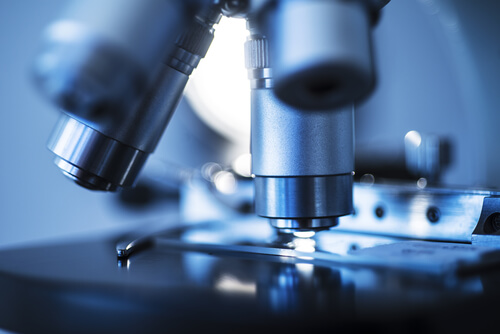
12
Dec