Most people have experienced the thrill of a fairground ride or roller coaster. The fear and adrenaline are something that is hard to replicate in any other way. So, when we consider the mechanical and engineering design of the ride, how can we be sure it is as safe as it can possibly be? In the past, the individual components and design has been soundly tested to ensure that the ride is structurally sound, and many tests and simulations are invented and applied to try to account for any eventuality. In addition, they are routinely tested every single day before use to ensure there is no mechanical fault or wear. So, how can 3D scanning help?
Can 3D Scanning Tech Be Used For Roller Coaster Accident Prevention And Maintenance?
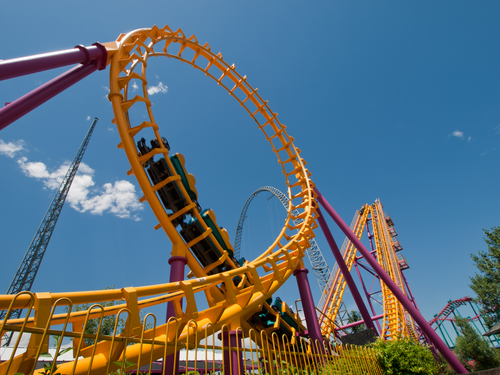
06
Aug