Torque is a type of force that tends to cause rotation. It is one of the most important mechanical quantities in many industrial applications. Precise measurement of the torque on rotating sections, placing high demand on test bench users and manufacturers. There are a couple of ways to determine torque:
Direct And Indirect Torque Measurement Techniques In Drive Train Technology
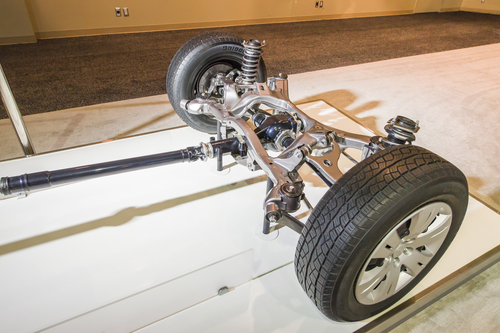
03
May