The Coordinate Measuring Machine, otherwise referred to as the CMM is a familiar tool in manufacturing facilities. It stands out as one of the most effective and reliable tools used in quality control. Used for three dimensional measurement and verification, CMMs come in different designs and of course brands. This makes it hard for a manufacturer with little or no knowledge on CMMs to buy one. There are however, factors that can make the whole buying process easy. Such factors include:
How Should Manufacturers Approach Buying CMMs?
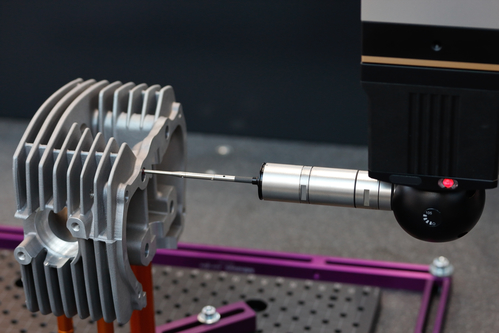
27
Oct