At the most basic level, manual gages are designed to make it easier to stage and gage a workpiece, ensure the best possible performance for the measuring task at hand, and reduce operator error. With this type of fixturing, the technician does not need to expend a significant amount of effort and time to complete the task. Today’s manufacturing operations are fast-paced. Those operations are also based on short runs of precision parts and flexibility. That is why using a gaging system that matches the way components are made is highly recommended. Here are further ways to simply gaging processes:
How To Simplify Gaging Processes
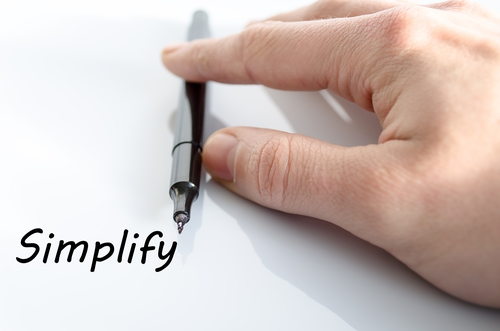
30
Oct