Today, a great array of internal precision machining operations is now facilitated via diamond or hard-metal tipped cutting tools. In addition, tool holders are available in various forms to suit the specific machining requirements. Now, factors such as the service lifespan of the cutting tool, the dimensional accuracy of the workpiece, and surface quality are affected by the material properties of the toolholder. If you do not get them right and need to facilitate a deep-hole machining procedure, you may encounter excessive vibration issues in the tool shaft. This can happen if there is a high degree of overhang; you will get that undesirable chattering. Let’s find out more about vibrations and how you can minimize them.
How To Minimize Vibration Tendencies In Machining Procedures
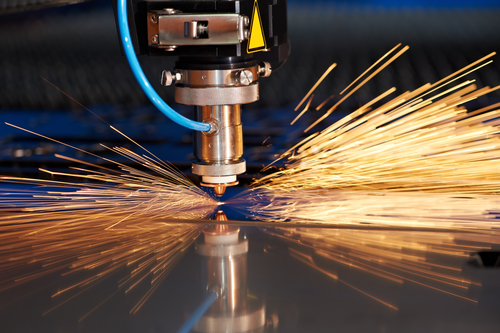
15
Jul