Liquid-filled gages are the most preferred choices for process environments requiring high physical stress because they are capable of protecting those environments from shock and vibration. Installing one requires a lot of careful though and consideration, on top of which, is making sure that the gauge is filled with the appropriate amount of liquid to be used for that particular application. Take note that silicone and glycerin should not be used when filling pressure gages where there are strong oxidizing agents. Additionally, venting these gages will relieve internal case pressure before use. The question is how are they usually vented?
How Are Liquid-Filled Gages Usually Vented?
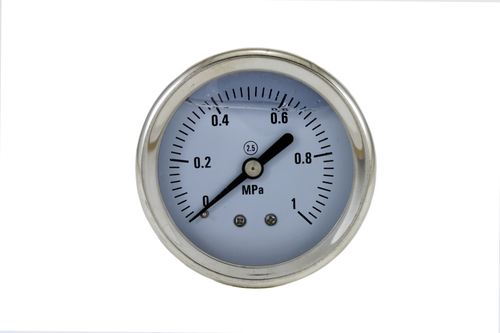
30
Jun