Product manufacturers and companies that produce building materials such as housewrap, fiberglass, flooring, fiberglass, wallboard, shingles, cores, and tubes can derive great benefits from shaft alignment of their machine equipment. There are many advantages associated with precision alignment of process lines and machine components.
Why Machine Alignment Is Beneficial To Building Product Manufacturers
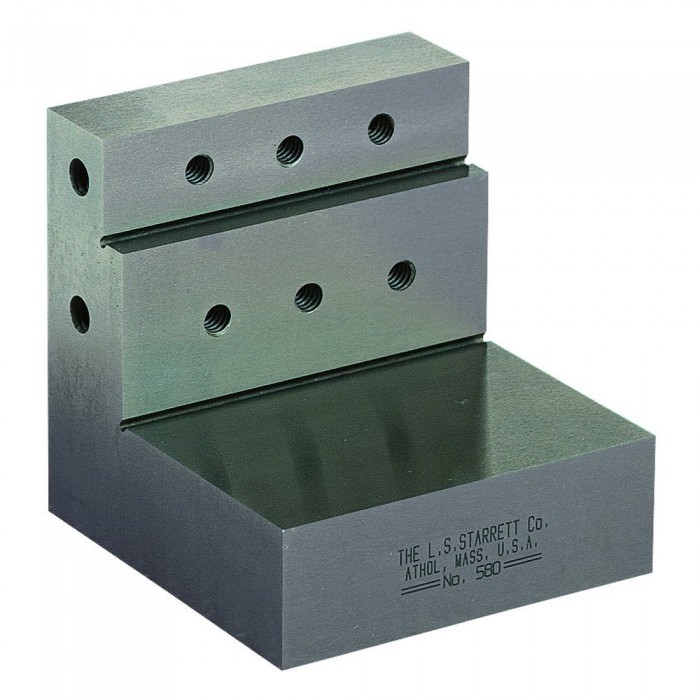
21
Feb