A force gage is a comprehensive solution for a component of a larger test system or specific tests. It can be easily integrated into a motorized or manual test stand, or it can even be handheld. It is straightforward for hand operated tests, and at the same time complicated enough to be integrated with motorized test stands, data collection software, and PLCs. They are commonly used in production, quality control, and research environments.
Work With Digital Force Gages Like A Pro
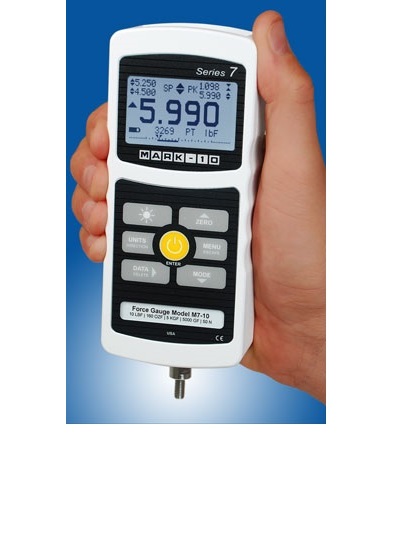
25
Feb