To automate a process, technical feasibility is a necessary prerequisite. This is the most important factor about automation to consider when automation is taken into account. Another precondition is the cost for development and deployment of both the software and hardware for automation. Labor cost and supply-demand dynamics also play an important role. The most important component in successful deployment over a period of time is the effort in adapting technology with human capital. With transformation of each individual workflow, every job will be changed, eventually. This requires change in skills as well as mind-sets.
Deciding Which Degree Of Automation You Prefer On Your Manufacturing Floor
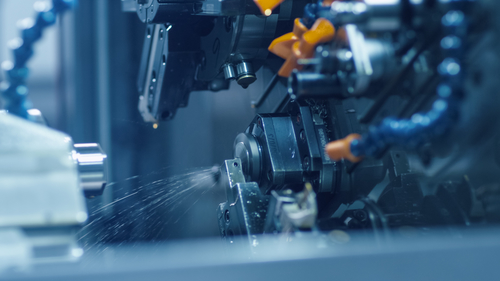
06
Mar