Air gaging works according to a law of physics that states pressure and flow are directly proportionate to clearance, which then react inversely to each other. This means that when clearance decreases, air flow and air pressure also decrease and increase respectively. When clearance increases, air flow and air pressure will increase and decrease proportionately. This is usually accomplished by regulating air flow via some sort of restriction. Two common options include a jeweled orifice or a needle valve. With that in mind, one will be able to increase back pressure and reduce air flow by bringing the workpiece (the obstruction) closer to the nozzle. If the nozzle becomes completely obstructed, there will be zero flow. Regulated air and back pressure will also be at the same level.
Understanding How Air Gaging Works
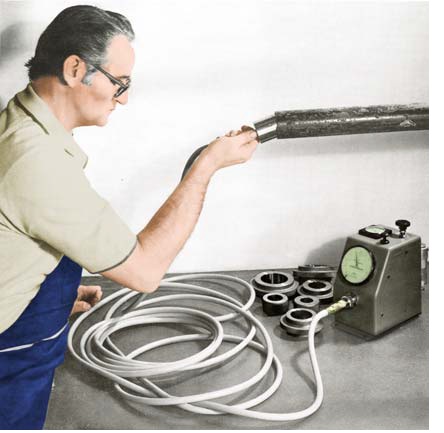
24
Dec