Thread-setting plugs play a vital role in measuring and confirming the accuracy of threaded components. Over time, these plugs may experience wear or damage, which can impact their precision. Regular thread setting plug calibration is necessary to certify that your measurements remain within the desired tolerances. Calibration not only extends the life of the tool but also prevents costly errors in manufacturing and assembly.
- Air Gages
- Bore gages
- Calipers
- Calibration Equipment
- CMMs Coordinate Measuring
- CMM Sensors, Probes & Styli
- Computed Tomography – CT Scanners
- Concentricity Gages
- Contour Measurement
- CUSTOM GAGES & FIXTURING
- CYLINDRICAL GO / NO GO / MASTERS
- Data Collection & SPC
- Depth Gages
- Fixtures & Part Holding CMM, Vision, Optical
- Force & Torque Gages
- Gage Blocks
- Gear & Spine Measurement
- GRANITE SURFACE PLATES, SQUARES & PARRALLELS
- HARDNESS TESTERS
- Height Gages
- HEX, HEXALOBE GAGES & SQUARE GAGES
- ID / OD GAGES & SNAP GAGES
- Indicators & Comparator Stands
- Laser Micrometers
- Layout and Shopfloor
- MICROMETERS
- MICROSCOPES & BORESCOPES
- Optical Comparators, Overlay Charts and Readouts
- Robotics and Automation
- ROUNDNESS & FORM
- SHAFT MEASUREMENT
- Structured Light 3D Analysis
- Surface Roughness Testers
- Thread Gages
- Video Measuring Machines
Company News
5 Thread Setting Plug Applications You Need To Know
Thread setting plugs are precision tools designed to measure and verify threaded holes and bolts. These vital instruments verify that threaded components meet industry standards and function as intended. If you work in manufacturing, maintenance, or quality control, understanding how thread-setting plugs work can help you maintain quality in your projects. Below, we explore the top thread setting plug applications that professionals rely on to achieve accuracy and precision.
When And Why Should You Use Thread Ring Gages?
Thread ring gages are fundamental tools used in the manufacturing and inspection of threaded parts. They allow for precise measurement of male threads to confirm they meet required specifications. In this article, we’ll discuss why thread ring gages are important, how they work, and when they should be used to ensure the correct fit and function of threaded components. Lastly, we’ll cover where to shop thread ring gages.
Tips For Picking A Professional-Grade Shaft Measuring Tool
When it comes to precision manufacturing, measuring the dimensions of shafts and other rotationally symmetrical workpieces accurately is a must. With increasing demands for smaller features, tighter tolerances, and faster production times, choosing the right shaft measuring tools can significantly impact the quality control process. In this guide, we’ll discuss key considerations for selecting professional-grade shaft measuring tools and explore some top models on the market.
A Buyer’s Guide On The Best 3D Laser Scanners
3D laser scanning has revolutionized industries ranging from manufacturing to healthcare. As the market for these tools grows, it can be difficult to choose the best 3D laser scanners for your specific needs. This guide will walk you through the top options on the market today for your consideration.
Micro Hardness – Micro Vickers and Knoop micro test block
Dial Bore Gage Combination Kit Models 2,3,4,5
Gear and Spline Tooth Measurement System
Mahr Millimar C1202 Amplifier

Mantis Ergonomics Microscope’s
At Willrich Precision, we understand the importance of finding the right measurement solutions for your metrology needs. That’s why we offer Mantis Ergonomics, a range of products designed to improve comfort and productivity during inspections and measurements.
There are three different products to choose from:
ELITE-CAM HD STEREO MICROSCOPE
This variant features an internally integrated digital camera, allowing for effortless image capture and documentation. It offers simultaneous optical and digital viewing and comes with easy-to-use PC software for image capture in various formats. It is compatible with all Mantis Elite options and configurations.
ELITE STEREO MICROSCOPE
The Mantis Elite is a patented ‘eyepieceless’ stereo microscope that offers superb 3-D imaging and unparalleled comfort. It reduces operator fatigue, increases quality, and enhances productivity. With magnification options up to 20x, the Mantis Elite is the ideal stereo viewer for precision tasks that require magnification. It comes with switchable two-tube fluorescent lighting for high-intensity or suitable lighting.
COMPACT 3D STEREO MICROSCOPE
The Mantis Compact is a low-magnification visual inspection microscope that provides excellent 3-D imaging and freedom of head movement. With Vision Engineering’s patented eyepieceless technology, the Mantis Compact is perfect for a wide range of inspection, manipulation, or rework tasks that require magnification. It offers quick-change magnification options of 2x, 4x, 6x, and 8x.
All Mantis Ergonomics products can be customized with additional options and stands to meet your specific application requirements. Our team of experts will guide you through the selection process and provide the necessary support to ensure you have the right solution.
At Willrich Precision, we aim to establish long-term relationships with our customers. As an ISO-accredited company, we offer years of credibility and expert assistance for your inspection and measurement needs.
Contact us today to learn more about Mantis Ergonomics and how we can assist you in finding the perfect measurement solution for your needs.
Q Span Gauging Systems
Are you tired of tedious and error-prone manual gauging tasks in your manufacturing process? Willrich Precision, your dedicated metrology partner, is here to revolutionize your measurement needs with our Q-Span Gauging Systems.
Q-Span Gauging Systems are innovative mobile robotic workstations designed to automate part handling and gauging of critical dimensions in high-mix, small-batch manufacturing. They allow you to automate your existing manual gauges and gauging techniques, improving process control, reducing variability, eliminating data entry errors, and increasing capacity.
Here’s the Q-Span Gauging functionality:
Each Q-Span Workstation is configured with a collaborative robot from Universal Robots, New Scale’s smart gripper/calipers, and teachable “plug-and-produce” software for zero-code programming. You can easily incorporate your preferred metrology tools, including calipers, thread gauges, height gauges, LVDT probes, bore gauges, vision systems, and more.
These systems automatically pick parts, measure multiple features on each part using automated gauges, and sort or place each part based on measured dimensions. They also record all measured data to a PC for statistical analysis, allowing you to digitize inspection data from multiple gauges into one output.
By implementing Q-Span Workstations, you can elevate your quality teams and tackle workforce challenges. With automated production processes, you can improve skills, capacity, productivity, recruitment, and retention.
At Willrich Precision, we are committed to providing you with the right solutions to meet your measurement needs. Whether you require standard gaging solutions or complex turnkey solutions, we’re here to help. Contact us today to start.
3 Functions of Fowler Bowers XT Holematic Groove Sets
We are excited to introduce the Fowler Bowers XT Holematic Groove Sets. These sets are designed to meet the demands and challenges of internal groove diameter measurement, offering exceptional precision and reliability.
The main 3 functions of the Fowler Bowers XT Holematic Groove Sets include:
- Fast and efficient measurements: with self-centering, 3-point heads, these sets provide exceptional repeatability. Additionally, they offer a resolution of 0.00005″/.001mm, ensuring accurate measurements and direct in/mm conversion.
- These groove sets cover a wide range of diameters: from 1/4″ to 4″ or 6 – 100mm, making them suitable for various applications. They also come with error-free Bluetooth data transfer, ensuring seamless connectivity for data sharing and analysis.
- Built to withstand harsh environments: the XT Holematic Groove Sets are IP67 protected against fluids and dust. This durability ensures reliable performance even in challenging production environments.
To cater to diverse needs, the XT Holematic Groove Sets include anvil profiles that suit common groove sizes. They also come with depth stops and UKAS-certified setting rings for accurate and standardized measurements. Furthermore, if your application requires special sizes, profiles, or depth extensions, Willrich can provide tailor-made solutions to measure any bore feature.
Order Today: https://willrich.com/product/fowler-xt-holematic-groove-sets/
Automate in 2024 | Boost ROI + Alleviate Bottlenecks
Are bottlenecks causing delays in your QC process?
By automating your QC process, you can alleviate bottlenecks and improve efficiency. At Willrich Precision Instrument, a dedicated metrology house with over 51 years of experience, we understand the importance of automation in streamlining your QC process.
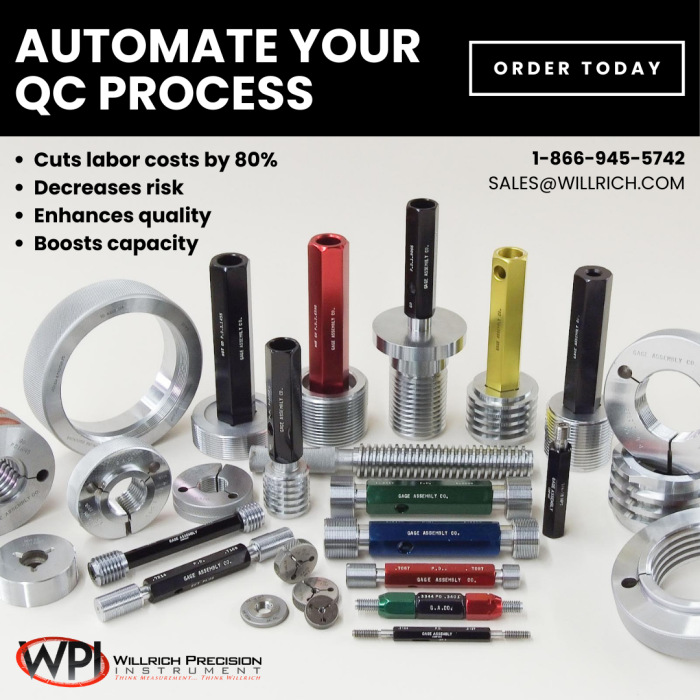
Why should you automate your QC process?
Manual gauging is labor-intensive and can significantly slow down production. Additionally, being understaffed or relying on outdated processes and slow equipment like a CMM can further hinder your operations.
Automating manual gauging can help reduce or even eliminate bottlenecks in manufacturing processes. In-process manual gauging can slow down machine cycles and result in idle spindle time, affecting machine output. Automated gauging systems can streamline this process and ensure accurate measurements. In the case of incoming inspection, an automated gauging system can help avoid delays and bottlenecks caused by limited resources and the need for inspection of outsourced parts.
Is automation worth the investment?
It is definitely worth the investment, as it offers numerous benefits that can be quantified with a return on investment (ROI) calculation.
By automating manual gauging processes in manufacturing, companies can experience reduced labor costs, decreased risk, higher levels of quality, and increased capacity. A practical example demonstrates how automation can lead to significant cost savings. For instance, if a medical device manufacturer employs two full-time QC inspectors to measure small parts manually, it costs them $3,360 per week in labor. However, by implementing automation technology, the labor cost for part measurement can be reduced by at least 80%, resulting in savings of $2,688 per week.
With the estimated implementation cost of $125,000, the full payback period for this investment is under a year. Beyond the payback period, the ROI is significant. Over three years, the investment can result in a 300% return, paying for itself three times over.
At Willrich Precision, we offer a wide range of metrology products, from sophisticated scanners to basic measuring tools, ensuring that we have the right solution for your dimensional inspection needs.
Don’t let bottlenecks hold you back. Automate your QC process with Willrich Precision Instrument and experience the benefits of increased efficiency and improved ROI.
Visit our website and explore our comprehensive range of solutions today!
Creaform’s MAX Series
Experience precision like never before with Creaform’s MAX Series, available exclusively through Willrich Precision.
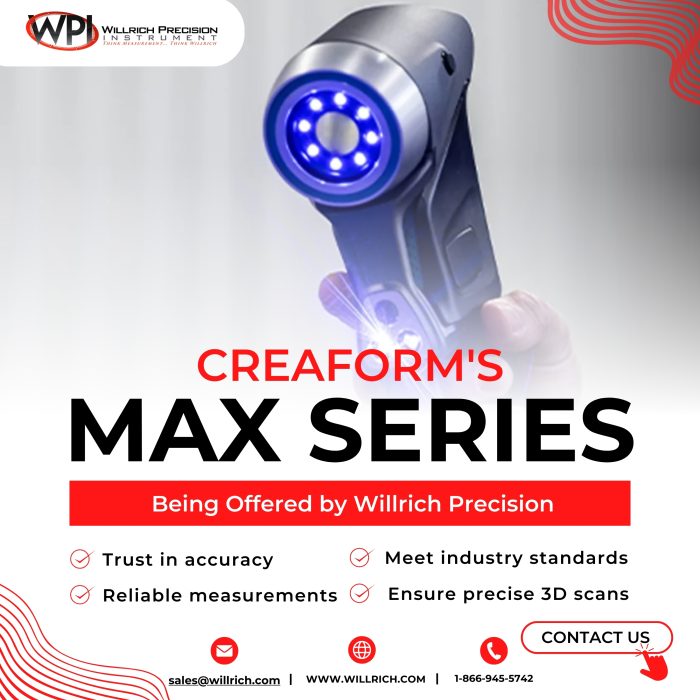
The MAX Series redefines the landscape of large and intricate surface measurements, making them more accessible than ever, now offered by Willrich Precision.
With Willrich Precision as your trusted source, you gain access to the MAX Series, allowing you to accurately measure large parts and assemblies (up to 15m!) in industries such as aerospace, transportation, energy, mining, and more.
Our MAX Series, manufactured by Creaform, guarantees exceptional metrology-grade precision (0.100 mm + 0.015 mm/m) with ISO 17025 accreditation, meeting VDI/VDE 2634 part 3 standards. Its dynamic referencing algorithms enable precise 3D scanning in various environments, making it an ideal solution for quality control, tight tolerances, and reverse engineering of large parts.
Request a FREE demo with Willrich Precision by contacting us 1-866-945-5742 or email us at [email protected]